- 1. What Is Kanban? The Ultimate Guide to Kanban Methodology
- 2. The Core Kanban Principles and Practices
- 3. What Is a Kanban Board? Examples and Usage Guide
- 4. Everything You Need to Know About Kanban Cards
- 5. Ultimate List of Kanban Tools and Software
- 6. Practical Kanban Templates and Examples
- 7. The Complete Guide to Personal Kanban
- 8. Kanban WIP - Work In Progress Limits Explained
- 9. What Is a Kanban Retrospective Meeting?
- 10. Kanban vs. Scrum Comparison Guide
- 11. Glossary of Kanban Project Management Terms
- 12. FAQs
- 1. What Is Kanban? The Ultimate Guide to Kanban Methodology
- 2. The Core Kanban Principles and Practices
- 3. What Is a Kanban Board? Examples and Usage Guide
- 4. Everything You Need to Know About Kanban Cards
- 5. Ultimate List of Kanban Tools and Software
- 6. Practical Kanban Templates and Examples
- 7. The Complete Guide to Personal Kanban
- 8. Kanban WIP - Work In Progress Limits Explained
- 9. What Is a Kanban Retrospective Meeting?
- 10. Kanban vs. Scrum Comparison Guide
- 11. Glossary of Kanban Project Management Terms
- 12. FAQs
How To Use Kanban in SAP
Kanban in SAP can be a great tool in optimizing material consumption, reducing production times, and enhancing team and organizational productivity.
Kanban boards give a clear picture of potential bottlenecks or missing parts and can be conveniently accessed by both the supply and demand sources.
Bringing together Kanban and SAP helps your team maintain a consistent production flow while minimizing any disruptions.
What is SAP?
SAP is a widely-used enterprise resource planning software that lets teams organize their business management using hundreds of integrated modules.
SAP is a centralized work management tool that lets companies share data and collaborate to enhance organizational outcomes.
Why use Kanban for SAP?
The conventional Material Requirements Planning (MRP) procedures calculate production quantities and delivery dates according to customer requirements and the information obtained from the bill of materials.
Work tasks are completed based on the “push” principle that may lead to longer production lead times or high inventory stocks.
Introducing Kanban helps set up a simple “pull” principle in which demand sources request material from the supply source only when required.
Kanban supplies materials only once the previous lot is exhausted, leading to faster deliveries, optimum inventory levels, and reduced production lead times.
How to use Kanban for SAP?
Kanban in SAP is primarily used to control material flows in production. Here is a typical workflow that demonstrates how Kanban can be used in SAP:
- Based on the pull principle, the demand source requests material from the preceding supply source or department only when it is needed.
- A Kanban control cycle is created with a fixed number of Kanbans (or cards) flowing from the demand center to the supply center. One Kanban is a predefined quantity of material to be supplied.
- Once a Kanban is empty, it is declared EMPTY and sent for the refill to the supply source. Then, the supply center starts producing the material quantity to fill it and sends it back to the demand source that confirms receipt by labeling it as FULL.
- Total production quantity includes the number of Kanbans completed in a defined time frame.
- Replenishment frequency is calculated on the actual material consumption. Based on the material needs, Kanbans move in the cycle. If the demand is more, the Kanbans move faster. In situations of less or sluggish demand, they move slowly.
Different Kanban methods available for SAP
Based on nature, scope, and work demands, companies can implement production control by choosing from the four different Kanban procedures available. The four Kanban procedures are:
Classic Kanban – In this method, the supply source, demand source, and quantity delivered in one Kanban are all clearly defined. Replenishment is triggered only for the specified amount of material outlined in the Kanban control cycle.
Event-driven Kanban – In this Kanban method, replenishment is done based on actual material consumption and is not provided regularly. Instead, replenishments happen only when teams specifically request for them.
One-card Kanban – In this method, two different Kanban quantities are available in each production cycle. Inventory levels at demand are optimized as replenishment is triggered only when the Kanban in use is half empty.
Kanban with Quantity Signal – In this replenishment method, manual signals are not used. Instead, individual quantities are directly entered inside the system. After this, the next action is automatically calculated based on the actual demand and withdrawal quantity.
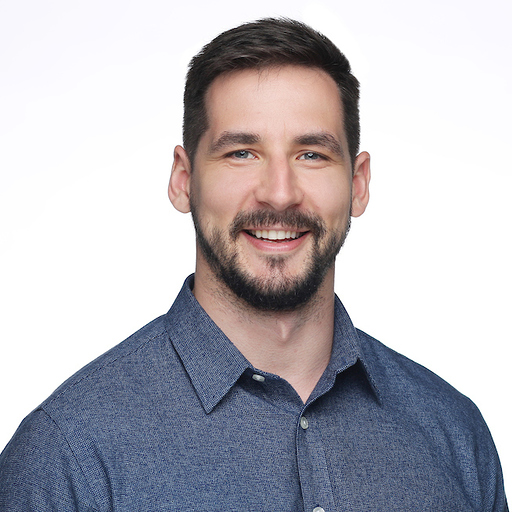
Alex Zhezherau
Alex is Wrike’s Product Director, with over 10 years of expertise in product management and business development. Known for his hands-on approach and strategic vision, he is well versed in various project management methodologies — including Agile, Scrum, and Kanban — and how Wrike’s features complement them. Alex is passionate about entrepreneurship and turning complex challenges into opportunities.